Are Forklifts Manual or Automatic? What Are The Differences?
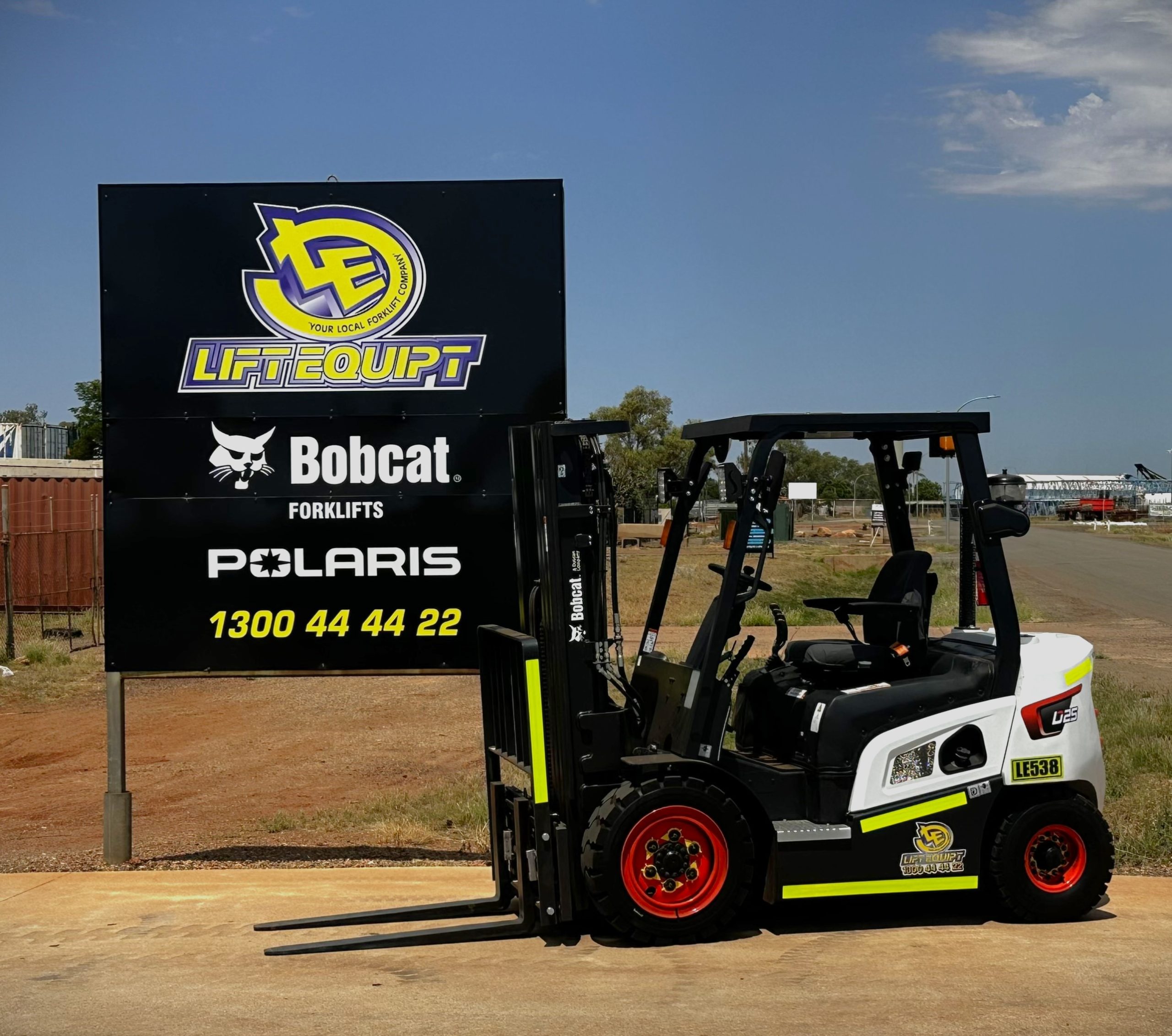
When it comes to moving materials, there’s a question that might stop a busy manager in their tracks: "Are forklifts manual or automatic?"
It turns out that the answer is both. So, which is best for your business?
Whether you're managing a bustling warehouse in Perth or overseeing mining operations in Karratha, understanding the differences between manual and automatic forklifts is crucial for business success.
Understanding Forklift Transmission Types
It’s essential to familiarise yourself with the various types of forklifts available.
Manual Transmission Forklifts
Manual forklifts require operators to shift gears using a clutch pedal and gear stick, much like a manual car. These machines typically feature 3-4 forward gears and 1-2 reverse gears.
The manual transmission gives operators complete control over power distribution and speed management.
Automatic Transmission Forklifts
Automatic forklifts use torque converters and planetary gears to handle gear changes automatically, allowing operators to focus on load management. Most have 2-speed or 3-speed transmissions with electronic control units.
Did you know? Electric forklifts are rapidly gaining popularity as the fastest-growing segment, driven by the push for sustainability. Check out our Bobcat series.
Looking to upgrade your fleet? We offer forklifts for hire and sale in Perth and Karratha.
Industry-Specific Applications
Choosing the right mix of manual and automatic forklifts depends on specific operational needs and conditions.
Warehousing and Distribution
Automatic forklifts boost efficiency in modern warehouses, providing consistent performance for high-volume operations.
Benefits include:
- 24/7 operational capability
- Reduced handling time
- Precise navigation in controlled environments
- Real-time inventory management
Manufacturing and Production
Manual forklifts excel in manufacturing settings requiring precise control and adaptability.
Key applications:
- Just-in-time parts delivery
- Custom material handling
- Precise placement in tight spaces
- Flexible response to production changes
Mining and Construction
Both forklift types have roles in demanding mining and construction sites:
Manual forklifts are ideal for:
🚜 Navigating rough terrain
📦 Handling variable loads
🔄 Adapting to changing conditions
❄️ Operating in extreme weather
Automatic forklifts offer:
🚚 Consistent transport between fixed points
👷 Reduced operator fatigue
⚠️ Enhanced safety in hazardous zones
Technical Specifications and Performance
Power Output and Efficiency
Skilled operators can make manual forklifts more fuel-efficient by optimising gear shifting and engine performance. However, this advantage depends on the operator's expertise. Automatic forklifts offer consistent fuel consumption regardless of who operates them.
Load Handling Capabilities
Both types handle similar maximum loads:
- Standard Class 4 models: Up to 2.5 tonnes
- Heavy-duty Class 5 models: Up to 16 tonnes
- Specialised models: Beyond 36 tonnes
Did you know? Below 5-ton forklifts lead the Australian market with 51% share, while 6–30-ton models grow with e-commerce demand.
Detailed Cost Analysis
Initial Investment
Manual forklifts typically cost 10-15% less than automatic models. This difference between manual and automatic forklifts becomes significant when purchasing multiple units.
Operational Costs
Here is a comprehensive breakdown of annual operational costs:
Cost Factor |
Manual Forklifts |
Automatic Forklifts |
Fuel Consumption |
Lower with the skilled operation |
Consistent across operators |
Maintenance |
Higher frequency, lower cost |
Lower frequency, higher cost |
Training |
Extended program required |
Basic training sufficient |
Parts Replacement |
More frequent clutch replacement |
Less frequent but costlier repairs |
For a detailed breakdown tailored to your needs, talk with our experts at 1300 44 44 22. We're here to help you make the best decision for your operations.
Maintenance Requirements and Schedules
Here are some maintenance tasks to focus on:
Manual Transmission Maintenance
Manual forklifts require regular attention to the clutch and transmission systems:
- Every 500 hours: Inspect the clutch for wear and perform pressure testing.
- Every 1000 hours: Change the gear oil using manufacturer-recommended lubricants.
- Every 2000 hours: Inspect the transmission, including synchronisers and bearings.
Operators should perform daily checks of clutch pedal play and gear shifting. A technician should address any unusual sounds or resistance immediately.
Automatic Transmission Service
Automatic forklifts need precise fluid management and regular maintenance:
- Every 250 hours: Check fluid levels for proper viscosity and cleanliness.
- Every 1000 hours: Change filters in both main and secondary systems.
- Every 3000 hours: Inspect the torque converter for wear and efficiency.
Technicians should monitor electronic control systems, perform software updates, and calibrate sensors to ensure optimal performance.
Safety Considerations and Risk Management
Operator Safety Features
Modern forklifts enhance safety with advanced monitoring and control systems that reduce accident risks and improve efficiency. Key features include:
Load moment indicators: Monitor weight distribution and stability.
Advanced stability control: Use gyroscopic sensors for automatic adjustments.
Anti-rollback technology: Provide intelligent brake management and hill-start assistance.
These work alongside traditional safety elements like overhead guards and emergency shut-offs. Regular calibration maintains their effectiveness.
Accident Prevention Protocols
Automatic forklifts reduce operator accidents through simplified operation and automated safety features. However, a manual forklift has advantages in challenging conditions.
- Superior traction on wet or uneven surfaces.
- Better manoeuvrability in tight spaces.
- Enhanced operator awareness from direct mechanical feedback.
Did You Know? From 2017 to 2022, NSW recorded 1,538 forklift incidents—nearly 75% occurred in transport, manufacturing, construction, retail, and wholesale industries.
Expert Insights: Your Top Questions Answered
Q: What are the training requirements for manual versus automatic forklifts?
A: Manual forklifts require extensive training—40 hours of theory and 60 hours of practical instruction. An automatic forklift needs less training. Regular safety refreshers are essential for both types.
Q: Which operational environment suits manual or automatic forklifts better?
A: A manual forklift is ideal for precise control in varied tasks, while automatic forklifts excel in high-volume, consistent operations.
Q: What workforce skills are needed for operating manual and automatic forklifts?
A: Manual forklifts demand skilled operators with extensive training. Automatic forklifts can be operated with basic training.
Q: Should small or large businesses choose manual or automatic forklifts?
A: Small businesses may prefer manual forklifts due to their lower costs and flexibility. Larger operations might benefit from automatic forklifts, which are more efficient in handling large volumes.
The Ultimate Lift for Your Operational Success
Choosing between manual and automatic forklifts depends on your operational needs. Manual forklifts are cost-effective and offer precise control, while automatic models provide consistency and ease of use. Consider your requirements, budget, and goals when making this decision.
Lift Equipt is your trusted partner for lifting needs across Western Australia. With branches in Perth, Karratha, and Melbourne, we provide reliable equipment and expert advice to support your business.
Call us today on 1300 44 44 22, and let’s work together to improve your operations.